- Visibility 97 Views
- Downloads 9 Downloads
- DOI 10.18231/j.ijmr.2020.018
-
CrossMark
- Citation
Detection of Burkholderia cepacia in pharmaceutical products
- Author Details:
-
Marina Ramsis Fahmy *
-
Youssry El-Sayed Saleh
-
Mary Sobhy Khalil
Introduction
Burkholderia cepacia was identified as Pseudomonas cepacia before 1992 as the cause of onion rot (cepacia in Latin = onion). [2], [1] B.cepacia is Gram-negative bacilli, 1-5 μm in length and 0.5-1.0 μm in width, aerobic, free-living, motile non-lactose fermenting and produce catalase. [3] The genus Burkholderia belongs to the ß-subdivision of the phylum Proteobacteria. Since the genus name was first assigned, the taxonomy of the genus Burkholderia has undergone considerable changes and the genus now includes 22 validly described species: B.cepacia (the type species), Burkholderia caryophylli, Burkholderia mallei, Burkholderia pseudomallei, Burkholderia gladioli, Burkholderia plantarii, Burkholderia glumae, Burkholderia vietnamiensis, Burkholderia andropogonis, Burkholderia multivorans, Burkholderia glathei, Burkholderia pyrrocinia, Burkholderia thailandensis, Burkholderia graminis, Burkholderia phenazinium, Burkholderia caribensis, Burkholderia kururiensis, Burkholderia ubonensis, burkholderia caledonica, Burkholderia fungorum, Burkholderia stabilis and Burkholderia ambifaria. [4] The mortality rate of the patients infected by cystic fibrosis due to BCC is high percentage as 62-100%. [5] B.cepacia is an opportunistic pathogen, it is one of the most frequently isolated bacterial contaminants in pharmaceutical samples around the world. [2], [8], [7], [6] B.cepacia is able to survive and multiply in the presence of disinfectants. [9]
Recently, Food and Drug Administration [10] warned drug manufactures that Burkholderia cepacia can remain alive in non-sterile aqueous products leading to the development of resistance to preservative systems used to protect product formulations. Its detection in pharmaceutical manufacturing process is difficult and products recalls are recurrent . The most frequent reasons of contamination of pharmaceutical products include microbial contaminant of the water used in product development contaminated and poor preservative system. [11] Pharmaceutical grade water is critical material for equipment cleaning, as well as, ingredient water in drug products. [12]
The aim of this research is to trace the sources of contamination of pharmaceutical non-sterile aqueous preserved products and how to control it during the manufacturing operations.
Materials and Methods
Isolation
The samples collected for the analysis were taken from different sources provided from the pharmaceutical company such as:
a) A queous finished products, 213 batches were produced in 2 years. During this time, 22 bacterial isolates were sub- cultured and identified. The test method involves transferring 10 ml from the test sample to (90) ml sterile Tryptone Azolectin Tween (TAT) broth medium, 10 ml of the prepared sample were filtered, cultured on Tryptic Soy Agar (TSA) medium and incubated at 30°C -35°C for 3-5 days and another 10 ml were aseptically added to about 100 mL sterile trypticase soy broth containing 4% Tween 20 (TSBTW). After incubation at 30°C -35oC for 18-24 hours, 0.1 ml of TSBTW were transferred to the surface of Oxidation-Fermentation-Polymyxin-Bacitracin-Lactose agar medium (OFPBL) and Burkholderia cepacia selective agar (BCSA) agar plates inverted and incubate d at 30°C -35°C for 18-72 hours.
b) From filling machines and preparation tanks, before each prepared batch we sampled the final rinse from 10 points. The method of testing was membrane filtration and the agar used was Reasoner’s 2A agar medium (R2A) incubated for 5 days at 30°C-35°C.
c) Water system including water treatment station and Reverse Osmosis (R.O.) water station, the samples were collected for one year. During this time, 384 samples were tested, from these 35 samples showed growth were sub- cultured and identified. The test method used is membrane filtration technique.
Identification
Smears of fresh isolates were picked on slides and heat fixed and examined microscopically and by the routine bacteriological methods including: subculture in selective media, biochemical tests: indole test, [13] oxidase test, [14] catalase test, [15] gelatin hydrolysis, [16] Voges-Proskauer test, [17] methyl red test, [18] carbohydrate fermentation test, [19] API 20 NE and VITEK 2 system.
Disinfectant efficacy test
Using two disinfectants such as Tego (alkyl diazapetane) and Viragri plus (blend of glutaraldehyde and quaternary ammonium compound) against B.cepacia after contact time 15 minutes on 4 different surfaces (Ceramic, Epoxy, Stainless-steel and glass). [20]
Susceptible odd product
The current product formula contain the preservative methyl paraben 0.1%, propyl paraben 0.02% and cremophore 1%. The proposed formula are the same concentration of parabens but different concentrations of cremophore. These dilutions are inoculated with a known volume not more than 100 CFU/ml of Burkholderia cepacia.
Antimicrobial preservative efficacy test
Two modified formula from this product were proposed and the effect of their preservatives activity were tested against B.cepacia: Formula X: 0.25% cremo phore, no ethanol with parabens and Formula Y: 5% ethanol with parabens. [21]
Molecular characterization using 16S rRNA.
The 16S rRNA gene sequences of the studied bacteria was sequenced in Sigma Lab after which the sequences were blasted to GenBank database at the National center for Biotechnology Information (NCBI) and a phylogenetic tree was illustrated using Clustal omega website.
Results
Stage I
21 batches from aqueous finished products were produced, 19 batches out of 21 were rejected due to their contamination as shown in [Table 1].
The 19 samples were negative indole, positive catalase, negative gelatinase, negative VP, negative MR and positive oxidase except isolates (3F, 7F, 10F, 14F and 19F).
The contaminant organism isolated from 19 samples had the ability to ferment certain carbohydrates such as glucose, cellobiose, mannitol, mannose, sucrose and lactose and change the medium color from red into yellow due to acid production while the other carbohydrates such as arabinose, maltose and sorbitol cannot ferment them and the medium color was not changed.
The contaminant organism isolated identified as “Burkholderia cepacia” by using identification systems as API 20 NE strip and VITEK 2 system.
Stage II
a)- Bacterial samples obtained from tanks and machine filling.
Before each prepared batch we sampled the final rinse from 10 points (syrup tank – hold tank – buffer tank – pipe – 6 nozzles) so we have 210 samples depending on number of prepared batches in Stage I (21 F).
190 samples out of 210 were contaminated and identified as the same contaminant organism.
"Burkholderia cepacia" as in the aqueous finished products in Stage I although the washing and sanitization of these tanks and nozzles by ethyl alcohol 70%.
After these important findings, we conclude that the source of contamination by a percentage 90% is the machine preparation and hold tanks and the machine filling pipes and nozzles.
We should disinfect all of these sites by a new disinfectant which has a strong bactericidal effect especially on Burkholderia cepacia.
b)-Disinfectant efficacy test
Tego (Alkyl diazapetane) is used for the disinfection of floors, walls, work surfaces and process equipment and it is applied to the surface.
As the log reduction is more than 3 as the disinfectant Tego 2000 has a great bactericidal and fungicidal effect against organisms at 15 minutes on all surfaces, so it is recommended for using this disinfectant instead of ethyl alcohol 70% ([Table 2]).
Viragri plus is based on an optimized blend of glutaraldehyde and quaternary ammonium compound (QAC) in aqueous solution. It is a highly effective, non-oxidizing disinfectant specially formulated for use on cleaned surfaces in the sectors where biocidal activity is required like pharmaceutical industry applications.
As the log reduction is more than 3 as the disinfectant Viragri plus has a great bactericidal and fungicidal effect against organisms at 15 minutes on all surfaces ([Table 3]).
At the end of this stage we conclude that the rinsing with these two disinfectants on all the machine tanks and filling parts with planned rotation instead of ethyl alcohol 70% only will be the efficient solution to prevent the recurrence of all the contamination by Burkholderia cepacia.
Accordingly monitoring and examining the produced batches after this treatment is very important as shown in the third stage.
Stage III
Bacterial isolation from aqueous finished products.
In this Stage, after the examination of 93 samples from different products, the results showed that 90 syrup batches (samples) were clean, free from the contaminant organism and accepted for their release in the market, this is high percentage of success 96.7%. While a 3 samples (22F, 23F, 63F) showed yellow colonies on TSA medium, knowing that these 3 samples were from the same product.
Susceptible odd product
It was shown in [Table 4] that as the concentration of cremophore decrease the bacterial count also decrease and the use high concentration of cremophore 1% in the current formula hide the effect of preservatives which is susceptible to the contamination.
Consequently it was proposed to the Research and Development Department to prepare a trial batch from this product containing 0.25% of cremophore instead of 1%.
Antimicrobial preservative efficacy test
The results of these experiments in [Figure 1] showed that the formula X could not be contaminated with Burkholderia cepacia as compared with formula Y. The new formula X should be produced instead of current one to prevent the recurrence of contamination.
Stage IV
Bacterial Isolation from water system
From R.O. station, out of 144 samples, 13 samples (from return point) 9.02% were identified as "Burkholderia cepacia group" the rest were free from contaminantion.
From water treatment station, out of 240 samples, 22 samples (from storage tank) 9.16% were identified as "Burkholderia cepacia group" while the rest were free from contaminantion.
As the contaminant organism is the same isolated from finished products, machines and water stations, conclusively the main root cause of contamination was the WATER.
Bacterial Isolation from aqueous finished products
All the 99 produced batches were pure and show no growth on selective medium.
As conclusion after the water treatments, 100% of the finished products were clear, accepted, free from any contamination especially Burkholderia cepacia group and returned to the markets safely.
Molecular characterization 16S rRNA gene sequence of the studied bacteria sequenced as Burkholderia cepacia complex. Sequences were submitted to GenBank database at NCBI under accession number: MN610444. Phylogenetic relationship of this species was blasted with other closely related bacterial species present in GenBank and a phylogenetic tree was illustrated as shown in [Figure 2].
Discussion
Quality of pharmaceutical product were greatly affected by environmental factors during manufacturing operations. It is necessary to control all these factors including raw materials, primary packaging materials, preparation tanks and filling ma chines, water system and the finished product to achieve the quality standards. [23], [22]
Aqueous finished products such as syrups provide a suitable environment for the growth and survival of both pathogenic and non-pathogenic microorganisms. [24]
Bacterial contamination of drug manufacturing industry affect odour, colour, taste of the products thus rendering them unacceptable to the patients. [25] Two years ago, investigations showed that Burkholderia cepacia is a major contaminant in both sterile and non-sterile products in hospitals and pharmaceutical products. A review of U.S. FDA recall data from January (2012) to July (2012) found that 39% of contamination cases in non-sterile products were due to the presence of B.cepacia. [26]
The authors found an overwhelming bacterial contaminant in pharmaceutical products in the end of stage I and identified by API NE20 as Burkholderia cepacia and identified by VITEK 2 as Burkholderia cepacia group. Furthermore, when the isolate identified at its molecular level by 16S rRNA gene sequences techniques, the result obtained showed that this bacteria is Burkholderia cepacia complex (BCC).
High similarity of B.cepacia complex (BCC) (typically above 98%) are measured, [4] indicating that BCC species are phylogenetically very closely related. [2]
Several studies have indicated problems with misidentification of Burkholderia species using phenotypic methods. Recent taxonomic advances have demonstrated that B.cepacia is actually a cluster of at least seven closely related genomic species (or genomovars) now called the B.cepacia. Genomovars II, IV and V are now formally named Burkholderia multivorans, Burkholderia stabilis and Burkholderia vietnamiensis, respectively (with the species designation B.cepacia being reserved for genomovar I). All of which may cause infections among immunocompromised patients and other vulnerable individuals. A combination of phenotypic and molecular tests such as 16S rRNA are recommended for differentiation among the genomovars of the Burkholderia cepacia complex. [27]
Burkholderiaceae contributed by more than 80% to the major hazard that could be delivered to patients through drugs, [25] and this high percentage is in line with results found by the authors in Stage I.
Burkholderia cepacia is a clear pathogen[28] its infection can lead to lung dysfunction and death. [29]
To address these concerns, pharmaceutical and healthcare manufacturers initiate procedures to prevent contamination of non-sterile drug products such as sanitary design, equipment cleaning and environmental monitoring. [30]
The most probable root causes of contamination with Burkholderia cepacia in pharmaceutical industries are absence of cleaning validation studies, poor water system control and design, inadequate microbiological controls and using one type of disinfectant for long period of time. [25]
Excessive bacterial samples isolation from different sources run from the raw material, the packaging materials of these products and finally the machine preparation tanks and filling nozzles to investigate the source of contamination in aqueous products isolated in Stage I.
The results obtained in Stage II showed that the raw materials and primary packaging materials are not the source of contamination while the preparation tanks and machines filling are the source. Consequently, the authors doubted in the disinfectant used in machines cleaning procedures which was only ethyl alcohol 70%.
These results were in agreement with [26] about the causes of contamination with B.cepacia in pharmaceutical companies, insufficient cleaning procedures emphasizing the contamination of the preparation tanks and machines filling in addition the use of one type of disinfectant for long period of time was also a cause of contamination because unfortunately B.cepacia able to survive and multiply in the presence of disinfectants. [9]
Many pharmaceutical manufactures will routinely use two "in-use" disinfectants in a specified rotational sequence for the site disinfection program. [11]
The authors performed a disinfectant efficacy test of other non- oxidizing disinfectants as Tego (alkyl diazeptane) and Viragri (quaternary ammonium compounds) against the contaminant organism B.cepacia on different surfaces and different contact time as showed in Stage II.
The authors succeeded in providing finished products clean from the contaminant organism by a percentage reached to 96.7% after performing the rotation plan between all of these tested disinfectants for one year as shown in Stage III, but 3.3% were still contaminated by B.cepacia, knowing that this percentage was from the same susceptible contaminant product. So, the authors studied this product ingredients, its preparation and its formulation and found the presence of me thyl paraben and propyl paraben as preservative agents, cremophore act as solubilizing agent and some sweetening agents as sorbitol and glycerin. These findings are in line with[31] who said that the most common method for countering microbial contamination is the use of preservatives.
The capability of Burkholderia cepacia to grow in well preserved formulation requires that the organism does not corrupt the shelf life stability of the product. If an organism exists at small concentration at manufacture the non- sterile product and this organism has the capability to multiply in the product, its potential to degrade the shelf-life of the product is clear. This is certainly a real concern with Burkholderia cepacia and a prudent activity might well be challenge the preservative system of the non-sterile medication with this organism in addition to the compendial organism ordinarily used within antimicrobial effectiveness test.[32]
Pharmaceutical preparations are especially susceptible to microbial growth since of the nature of their ingredients. Such preparations are protected by the addition of anti-microbial agents in the formulation to devastate and repress the growth of those microorganisms that may contaminate the product during manufacturing or use. Among the most commonly used additive in the preservation of aqueous pharmaceutical preparations are methyl paraben because of their synergistic impacts. Parabens have been used as preservative for over 70 years.[33]
In the present study, the authors revealed finally that the cause of product susceptibility to contamination, the high concentration of cremophore (1%) hide the effect of preservatives. A modification in formula was suggested such as: Formula X: 0.25% cremophore instead of 1% with parabens and Formula Y: 5% ethanol with parabens. In Stage III these two formulas in addition to the current one undergo an antimicrobial preservative efficacy test especially against B.cepacia. Consequently the formula X could not be contaminated with B.cepacia as compared with formula Y. It was recommended that the production of formula X instead of the current one is more effective to prevent the recurrence of contamination.
Fortunately, the problem of contamination in machines was resolved by applying new disinfectants but the main source of contamination remained unknown. Further investigation in Stage IV, 384 samples from water treatment station and R.O. station were tested. Of these, 35 isolates were recovered and identified. B.cepacia was overwhelmingly the most common isolates from the purified water system. This conclusion was in agreement with about the most common source of contamination which is water and aqueous products are at very high risk due to the ability of Burkholderia cepacia to remain viable in stressful and hard conditions.
Water is widely used in pharmaceutical manufacturing either as a raw material, as an ingredient, or as a final product. Water is also used for rinsing equipment or for the preparation of disinfectants and detergents. These applications require pharmaceutical grade water to be used, which is water that has been through a chemical purification step. [34] Purified water is high grade water produced by Reverse Osmosis (R.O.). R.O. units use a semi permeable membrane to achieve microbial reductions. R.O. results by applying pressure to the concentrated side of the membrane. This pushes purified water into the dilute side. The rejected microorganisms from the concentrated side are then rinsed away. [35]
The authors proposed different protocols aiming to control and to prevent the contamination. These treatments stated in Stage IV are Ultraviolet (UV) disinfection, chemical washing with Ethylene di-amine tetra-acetic acid (EDTA), acidic and basic wash, thermal sterilization at 110 ˚C for 90 minutes, Ozone sterilization, hydrogen peroxide sanitization and chlorine disinfection.
UV radiation is inappropriate for water sanitization due to the presence of soluble organic materials that can react with or absorb the UV radiation, leading to the reduction of the disinfection performance. Practically, the applying of UV radiation has no effect on contamination. Chemical washing and thermal sterilization have very short effect on contamination, so, another water disinfection method should be applied such as: ozone sterilization used every week for R.O. loop feeding syrup production line. [35]
Ozone is the strongest oxidation agent in water treatment and purification and reuse has attracted great interest and is adding new aspects in ozonation-by product research. [38], [37], [36]
Studies showed the disinfection by ozone effectively kills pathogenic microorganisms such as Pseudomonas aeruginosa, Staphylococcus aureus and Burkholderia cepacia including bacteria growing in biofilms. Ozone is generally effective as a disinfectant but the results vary according to different factors such as: differences in the concentration of ozone, time of exposure along with different bacteria and growth conditions. [12]
The authors found that after 6 months of ozone disinfection, a recurrence of contamination was revealed. It is also an expensive disinfection technology operating costs and to date it has been used as a pre-disinfection treatment process for the destruction of organic micropollutants. Ozone is not stable so can’ t be produced and transported to the point of use. It must be generated at the point of use. A secondary disinfectant is required. [35]
Code | on OFPBL | on BCSA | Gram stain |
1F | yellow colonies | yellow colonies surrounded by pink zones | G-ve bacilli |
2F | yellow colonies | yellow colonies surrounded by pink zones | G-ve bacilli |
3F | yellow colonies | yellow colonies surrounded by pink zones | G-ve bacilli |
4F | yellow colonies | yellow colonies surrounded by pink zones | G-ve bacilli |
5F | yellow colonies | yellow colonies surrounded by pink zones | G-ve bacilli |
6F | Blue colonies | white colonies | G-ve bacilli |
7F | Blue colonies | white colonies | G-ve bacilli |
8F | Blue colonies | transparent colonies | G-ve bacilli |
9F | Blue colonies | transparent colonies | G-ve bacilli |
10F | Blue colonies | white colonies | G-ve bacilli |
11F | Blue colonies | transparent colonies | G-ve bacilli |
12F | Blue colonies | transparent colonies surrounded by pink zones | G-ve bacilli |
13F | Blue colonies | yellow colonies | G-ve bacilli |
14F | Blue colonies | yellow colonies | G-ve bacilli |
15F | yellow colonies | yellow colonies surrounded by pink zones | G-ve bacilli |
16F | yellow colonies | yellow colonies surrounded by pink zones | G-ve bacilli |
17F | yellow colonies | yellow colonies surrounded by pink zones | G-ve bacilli |
18F | yellow colonies | yellow colonies surrounded by pink zones | G-ve bacilli |
19F | yellow colonies | yellow colonies surrounded by pink zones | G-ve bacilli |
20F | No Growth | No Growth | - |
21F | No Growth | No Growth | - |
Organism | Positive control (CFU) | Recovery (CFU) | No. of log reductions |
Burkholderia cepacia | 8x108 | 5.6x104 | 4.15 |
Surface | Organism | +ve control (CFU) | Recovery (CFU) | No. of log reductions |
Ceramic | Burkholderia cepacia | 8.4x108 | 7.5x104 | 4 |
Epoxy | 2.5x104 | 4.5 | ||
Glass | 5x104 | 4.2 | ||
Stainless-steel | 6x104 | 4.1 |
Cremophore concentrations | 1% | 0.75% | 0.50% | 0.25% |
Methyl paraben | 0.10% | 0.10% | 0.10% | 0.10% |
Propyl paraben | 0.02% | 0.02% | 0.02% | 0.02% |
Burkholderia cepacia (CFU/ml) | 82 | 51 | 21 | 5 |
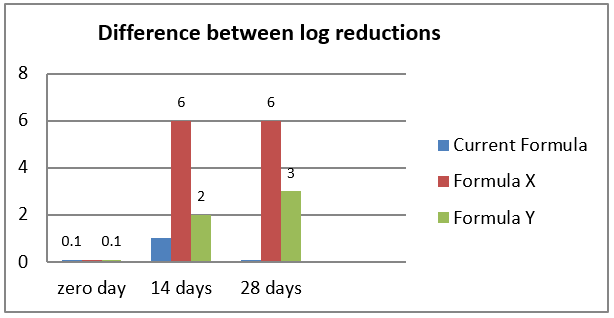
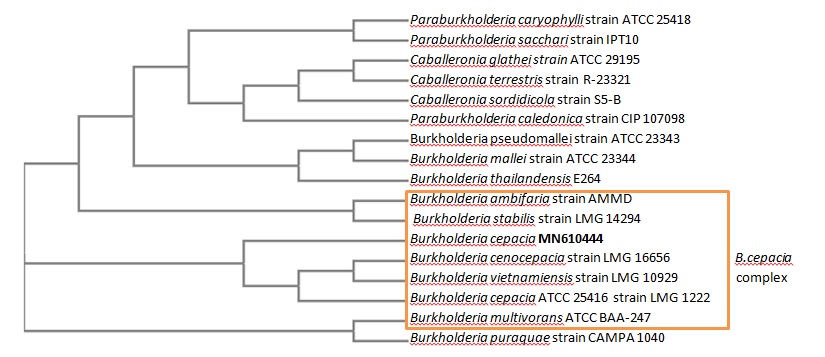
Other method for water disinfection was used which recommended by, [33] is the use of oxidizing disinfectants, this group includes oxygen-releasing components (peroxygens) like hydrogen peroxide (H2O2). They disturb the cell wall permeability, causing cytoplasm leakage and denature bacterial cell enzymes through oxidation. Oxidizing agents have advantages in that they clear and colorless, so they cannot stain the surface. [30]
Hydrogen peroxide 3% has been used for water disinfection and showed a strong bactericidal effect against B.cepacia.
The most common form of disinfection is chlorination, although ozone and UV light are also used. Chlorine continues to be one of the most effective disinfectant, it is relatively easy to handle, the costs of chlorine installation are low, simple to dose, measure and control and it has a relatively good residual effect. Chlorine is the most common form of water treatment used worldwide. Chlorine is widely available and can be applied in many forms and ways.[40], [39], [35]
After all these previous studies, our recommendation is the use of chlorine and hydrogen peroxide in water disinfection is the perfect method for its sterilization, while the ozone disinfection can be used only on surface machines.
At the end of Stage IV, 100% of the finished products shown in Stage IV were clear, accepted, free from any contaminant especially Burkholderia cepacia and returned to the markets safely.
[Figure 1] Antimicrobial preservative efficacy results showed in form of difference in log reductions between modified formula from the susceptible odd product formula X: 0.25% cremophore, no ethanol with parabens, formula Y: 5% ethanol with parabens and the current formula 1% cremophore with parabens at the applicable test intervals (zero day, after 14 days and after 28 days).
The log reduction is defined as the difference between the log10unit value of the starting concentration of CFU/ml in the suspension and the log10 unit value of CFU/ml of the survivors at that time point.
The log reduction calculated as:
Log reduction = log 10 (Total Positive Control count /Total Test Sample Count)
The results of these experiments showed that the formula X could not be contaminated with Burkholderia cepacia as compared with formula Y.
Conclusion
The characterization of the isolated organism was performed using various morphological, biochemical and physiological parameters and the result was Burkholderia cepacia group. Molecular characterization based on 16S rRNA and NCBI BLAST search confirms the identity of the test organism Burkholderia cepacia complex
Conclusively, it is recommended to prevent the contamination of the finished products during the process of manufacturing by:
The usage of different disinfectants which have strong effect on B.cepacia and a rotation plan between them is required.
The pharmaceutical water stations contaminated with this microorganism must undergo treatment by using 3% hydrogen peroxide and by chlorine disinfection up to 1ppm.
Source of Funding
None.
Conflict of Interest
None.
References
- W H Burkholder. Sour skin, “a bacterial rot. Phytopathol 1950. [Google Scholar]
- M A M Attia, A E Ali, T M Essam, M A Amin. A study on Burkholderia cepacia in susceptible pharmaceutical products: semi-nested PCR. PDA J Pharm Sci Technol 2016. [Google Scholar]
- Leang-Chung Choh, Guang-Han Ong, Kumutha M. Vellasamy, Kaveena Kalaiselvam, Wen-Tyng Kang, Anis R. Al-Maleki. Burkholderia vaccines: are we moving forward?. Front Cell Infect Microbiol 2013. [Google Scholar]
- T. Coenye, P. Vandamme, J. R. W. Govan, J. J. LiPuma. Taxonomy and Identification of the Burkholderia cepacia Complex. J Clin Microbiol 2001. [Google Scholar]
- M K Trivedi, S Patil, H Shettigar, M Gangwan, S Jana. An effect of biofield treatment on multidrug-resistant Burkholderia cepacia: a multihost pathogen”. Trop Med Infect Dis 2015. [Google Scholar]
- P Vandamme. Burkholderia cepacia:Pandora's Box redefined. BCCM News 2001. [Google Scholar]
- L Jimenez. . Microbial Contamination Control in the Pharmaceutical industry” 2004. [Google Scholar]
- L. Torbeck, D. Raccasi, D. E. Guilfoyle, R. L. Friedman, D. Hussong. Burkholderia cepacia: This Decision Is Overdue. PDA J Pharm Sci Technol 2011. [Google Scholar]
- Neha Rastogi, Surbhi Khurana, Balaji Veeraraghavan, Francis Yesurajan Inbanathan, Suresh Kumar Rajamani Sekar, Deepak Gupta. Epidemiological investigation and successful management of a Burkholderia cepacia outbreak in a neurotrauma intensive care unit. Int J Infect Dis 2019. [Google Scholar]
- . FDA 2017; updates on Burkholderia cepacia contamination. . [Google Scholar]
- Huy Dao, Prit Lakhani, Anitha Police, Venkataraman Kallakunta, Sankar Srinivas Ajjarapu, Kai-Wei Wu. Microbial Stability of Pharmaceutical and Cosmetic Products. AAPS Pharm Sci Tech 2018. [Google Scholar]
- Dana Towle, Vanisha Baker, Craig Schramm, Matthew O'Brien, Melanie S. Collins, Richard Feinn. Ozone disinfection of home nebulizers effectively kills common cystic fibrosis bacterial pathogens. Pediatr Pulmonol 2018. [Google Scholar]
- Mercedes Alsina, Anicet R. Blanch. Improvement and update of a set of keys for biochemical identification of Vibrio species. J Appl Bacteriol 1994. [Google Scholar]
- K J Steel. The Oxidase Reaction as a Taxonomic Tool. J Gen Microbiol 1961. [Google Scholar]
- Welton I. Taylor, David Achanzar. Catalase Test as an Aid to the Identification of Enterobacteriaceae. Appl Microbiol 1972. [Google Scholar]
- M.N. Preobrazhenskaya, E.G. Balashova, K.F. Turchin, E.N. Padeiskaya, N.V. Uvarova, G.N. Pershin. Total synthesis of antibiotic indolmycin and its stereoisomers. Tetrahedron 1968. [Google Scholar]
- B. E. Eddy, G. S. Borman, W. H. Berkeley, R. D. Young. Tumors Induced in Hamsters by Injection of Rhesus Monkey Kidney Cell Extracts. Exp Biol Med 1961. [Google Scholar]
- V Ljutov. Technique of methyl red test. Acta Pathol Microbiol Scand Banner 1961. [Google Scholar]
- A N N E Reddick. A simple carbohydrate fermentation test for identification of the pathogenic Neisseria. J Clin Microbiol 1975. [Google Scholar]
- Rock-ville. . United States Pharmacopeia. USP 42, chapter (1072) Disinfectants and antiseptics. United States Pharmacopeial Convention 2019. [Google Scholar]
- Rock-ville. United States Pharmacopeia. USP 42, chapter (51) Antimicrobial effectiveness testing. United States Pharmacopeial Convention. 2019. [Google Scholar]
- N Kumar, A Jha. Temperature excursion management: A novel approach of quality system in pharmaceutical industry”. Saudi Pharm J 2017. [Google Scholar]
- S A D I A Khanom, K K Das, S O U R A V Banik, R A S H E D Noor. Microbiological analysis of liquid oral drugs available in Bangladesh”. Int J Pharm Sci 2013. [Google Scholar]
- M E Eissa. Distribution of bacterial contamination in non-sterile pharmaceutical materials and assessment of its risk to the health of the final consumers quantitatively. Beni-Suef Univ J Basic Appl Sci 2016. [Google Scholar]
- M Ali. Burkholderia cepacia in Pharmaceutical Industries”. Int J Vaccines Vaccination 2016. [Google Scholar]
- M B Francesch. B.cepacia: what is it and why is it a concern?. 2019. [Google Scholar]
- D. A. Henry, E. Mahenthiralingam, P. Vandamme, T. Coenye, D. P. Speert. Phenotypic Methods for Determining Genomovar Status of the Burkholderia cepacia Complex. J Clin Microbiol 2001. [Google Scholar]
- E Torok, Ed Moran, F Cooke. . Oxford Handbook of Infectious diseases and microbiology”, second edition 2009. [Google Scholar]
- T Sandle, D Reber, M Griffin. Microbial Control and Identification. Burkholderia cepacia complex: Characteristics, products risks and testing requirements 2018. [Google Scholar]
- T Sandle. Sanitation of pharmaceutical facilities. J GXP Compliance 2014. [Google Scholar]
- R C Moreton. Commonly used excipients in pharmaceutical suspensions. Pharmaceutical Suspensions 2010. [Google Scholar]
- S Sutton. What is an objectionable organism. Am Pharm Rev 2012. [Google Scholar]
- T Sandle. Microbiological monitoring of pharmaceutical water systems. Eur Pharm Rev 2017. [Google Scholar]
- Tim Sandle. Characterizing the Microbiota of a Pharmaceutical Water System-A Metadata Study. SOJ Microbiol Infect Dis 2015. [Google Scholar]
- S Achour, F Chabbi. Disinfection of drinking water-Constraints and optimization perspectives in Algeria”. LARHYSS J 2014. [Google Scholar]
- Shi-hong Qin, Li Cheng, Agbedor Lambert Selorm, Fa-ting Yuan. An Overview of Ozone Research. J Adv Oxidation Technol 2018. [Google Scholar]
- Keisuke Ikehata, Yuan Li. . Ozone-Based Processes 2018. [Google Scholar]
- K Ikehata. Recent Research on Ozonation By-products in Water and Wastewater Treatment: Formation, Control, Mitigation, and Other Relevant Topics. Water and Wastewater Treatment Technologies 2019. [Google Scholar]
- G C White. . Handbook of Chlorination and Alternative Disinfectants, 3rd ed 1992. [Google Scholar]
- . . WHO/WEDC. “Measuring chlorine levels in water supplies, Technical notes on drinking-water, sanitation and hygiene in emergencies 2013. [Google Scholar]
- Introduction
- Materials and Methods
- Isolation
- Identification
- Disinfectant efficacy test
- Susceptible odd product
- Antimicrobial preservative efficacy test
- Molecular characterization using 16S rRNA.
- Results
- Stage I
- Stage II
- Stage III
- Bacterial isolation from aqueous finished products.
- Susceptible odd product
- Antimicrobial preservative efficacy test
- Stage IV
- Discussion
- Conclusion
- Source of Funding
- Conflict of Interest